Understanding Electric Injection Molding Machines
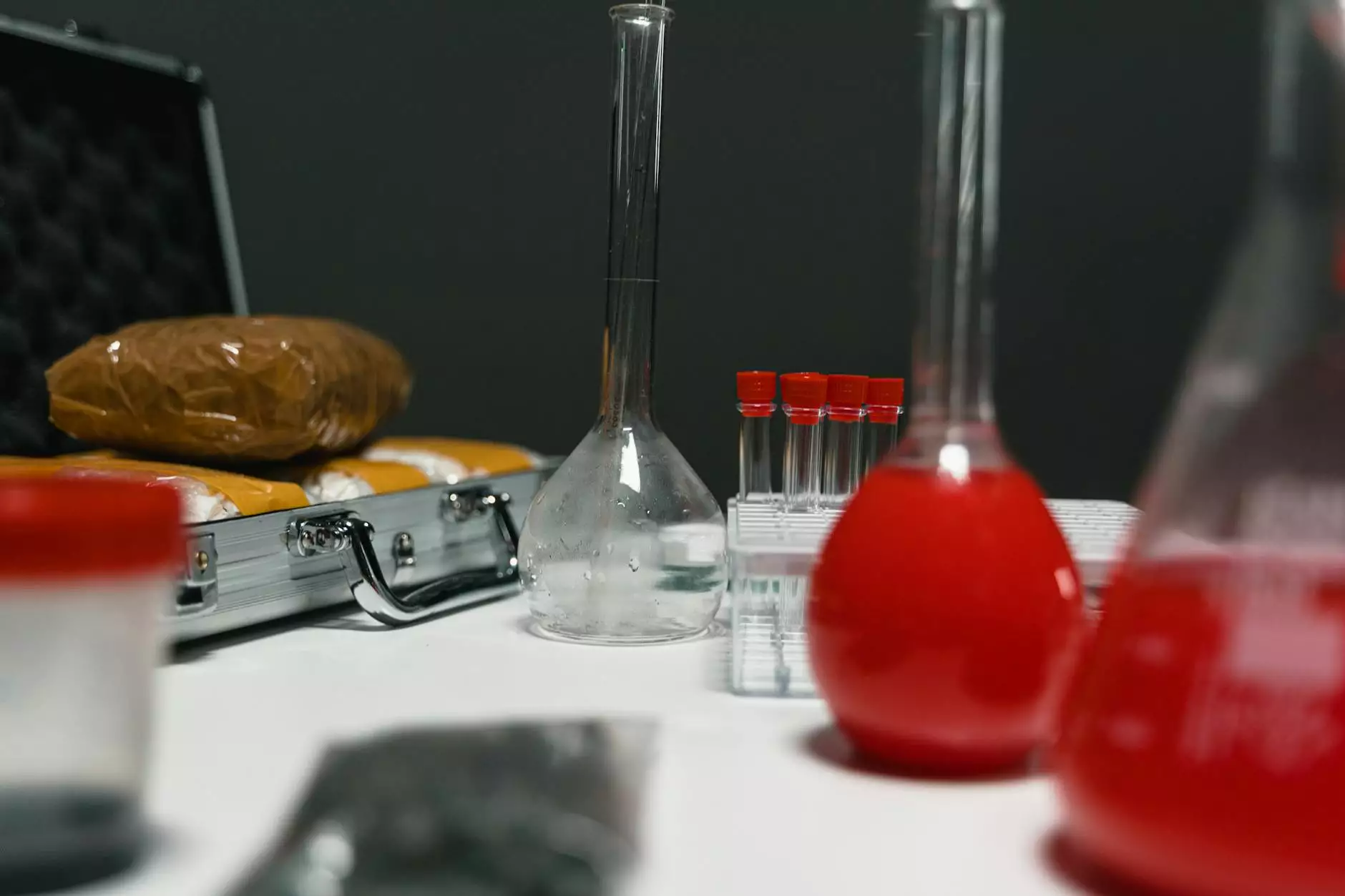
Electric injection molding machines have revolutionized the manufacturing landscape, particularly in metal fabrication. These machines offer precise control, enhanced efficiency, and an environmentally friendly approach to mold production. In this article, we delve into the intricacies of electric injection molding machines, exploring their features, advantages, applications, and the future they promise in the manufacturing domain.
What is an Electric Injection Molding Machine?
At its core, an electric injection molding machine is designed to produce plastic parts through the injection molding process. The process involves heating plastic pellets until they become molten, injecting this material into a mold, and allowing it to cool and solidify into the desired shape.
Unlike their hydraulic counterparts, electric machines leverage servo motors for movement and control. This technology offers a multitude of advantages that have propelled their adoption across various industries, especially in metal fabricators.
Key Features of Electric Injection Molding Machines
Electric injection molding machines come equipped with several notable features, which include:
- Precision Control: The use of servo motors allows for highly accurate movements, resulting in better precision during the molding process.
- Energy Efficiency: Electric machines consume significantly less power compared to hydraulic machines, making them more environmentally friendly and cost-effective.
- Faster Cycle Times: With quicker response times, electric machines can improve production efficiency significantly.
- Reduced Noise Pollution: Unlike hydraulic machines that often produce considerable noise, electric options operate more quietly, enhancing the work environment.
- Low Maintenance Requirements: Fewer components in electric systems translate to lower maintenance needs and reduced downtime.
The Benefits of Using Electric Injection Molding Machines
1. Enhanced Production Efficiency
One of the most compelling benefits of electric injection molding machines is their ability to enhance production efficiency. Thanks to their fast cycle times and precise control, manufacturers can achieve higher output levels, which is essential in today’s fast-paced market.
2. Consistent Quality in Production
Electric machines maintain consistent pressure and temperature throughout the injection process, minimizing the risk of defects. This results in a higher quality end product, which is crucial for industries such as automotive and consumer electronics.
3. Environmental Impact
In an era where sustainability is paramount, electric injection molding machines reduce energy consumption and waste. By using less energy and generating fewer emissions, they align with the global push for greener manufacturing practices.
4. Versatility in Application
The versatility of electric machines allows manufacturers to work with a wide range of materials, including various plastics and metals. This adaptability makes them ideal for diverse sectors, from healthcare to automotive.
Applications of Electric Injection Molding Machines
Electric injection molding machines are applicable across numerous sectors, contributing to innovations in product design and manufacturing. Some key applications include:
- Automotive Industry: Production of precise components such as dashboards, panels, and even complex assemblies.
- Electronics: Manufacturing of housings, connectors, and parts that demand high precision.
- Medical Devices: Creation of intricate devices and components that require strict adherence to quality standards.
- Consumer Goods: Production of everyday items like packaging, containers, and household appliances.
How Electric Injection Molding Machines Work
The operation of electric injection molding machines is based on several key steps:
1. Material Preparation
The process starts with the preparation of plastic granules, typically fed into the machine's hopper. The granules are then heated in a barrel until they melt into a molten state. This step is crucial for ensuring a uniform consistency in the material.
2. Injection Phase
Once the material is molten, it is injected into the mold cavity under controlled pressure. This phase is critical, as the pressure and speed of injection can significantly affect the final product's quality.
3. Cooling
After the material fills the mold, it must cool down to solidify. The cooling system within the mold assists in this process, minimizing the cycle time while ensuring the part retains its shape.
4. Ejection
Following adequate cooling, the newly formed part is ejected from the mold, completing the injection molding cycle. This step is designed to be as efficient as possible, reducing downtime and increasing output.
Choosing the Right Electric Injection Molding Machine
Selecting the appropriate electric injection molding machine for specific applications involves careful consideration of several factors:
- Production Volume: Determine the scale of production required and choose a machine that can handle it efficiently.
- Type of Material: Different machines may be better suited for specific types of plastics or additives.
- Mold Design: Consider the complexity and design of the mold itself. More intricate molds may require machines with advanced features.
- Budget: Evaluate the budget constraints against the features offered by various machines. Higher upfront costs may lead to savings in the long run through efficiency.
The Future of Electric Injection Molding Machines
As technology continues to advance, electric injection molding machines are expected to evolve alongside other manufacturing technologies. Several trends are likely to shape the future of these machines:
- Integration with Industry 4.0: The rise of smart factories will lead to greater integration of electric injection molding machines with IoT technology, enhancing monitoring and efficiency.
- Sustainability Innovations: Ongoing advancements in materials and energy efficiency will further mitigate the environmental impact of molding processes.
- Customization: Demand for more complex and customized parts will push manufacturers to continue developing more versatile machines.
- Advanced Automation: Automation technologies, such as robotics and AI, will further streamline the molding process, increasing production rates and efficiency.
Conclusion
Electric injection molding machines represent a leap forward in manufacturing technology. With their high precision, energy efficiency, and environmental benefits, they have established themselves as a vital asset in various industries including metal fabricators. As manufacturers continue to seek efficient and sustainable solutions, the role of electric injection molding machines will only grow. Investing in these advanced machines is not just a choice; it is a strategic advancement toward a more prosperous and sustainable future in manufacturing.
Discover More at DeepMould.net
For those looking to learn more about electric injection molding machines or to explore options for enhancing your manufacturing processes, visit DeepMould.net. Our team of experts is dedicated to providing innovative solutions tailored to your specific needs. Let us help you transform your manufacturing capabilities today!