The Essential Guide to CNC Machining Factories
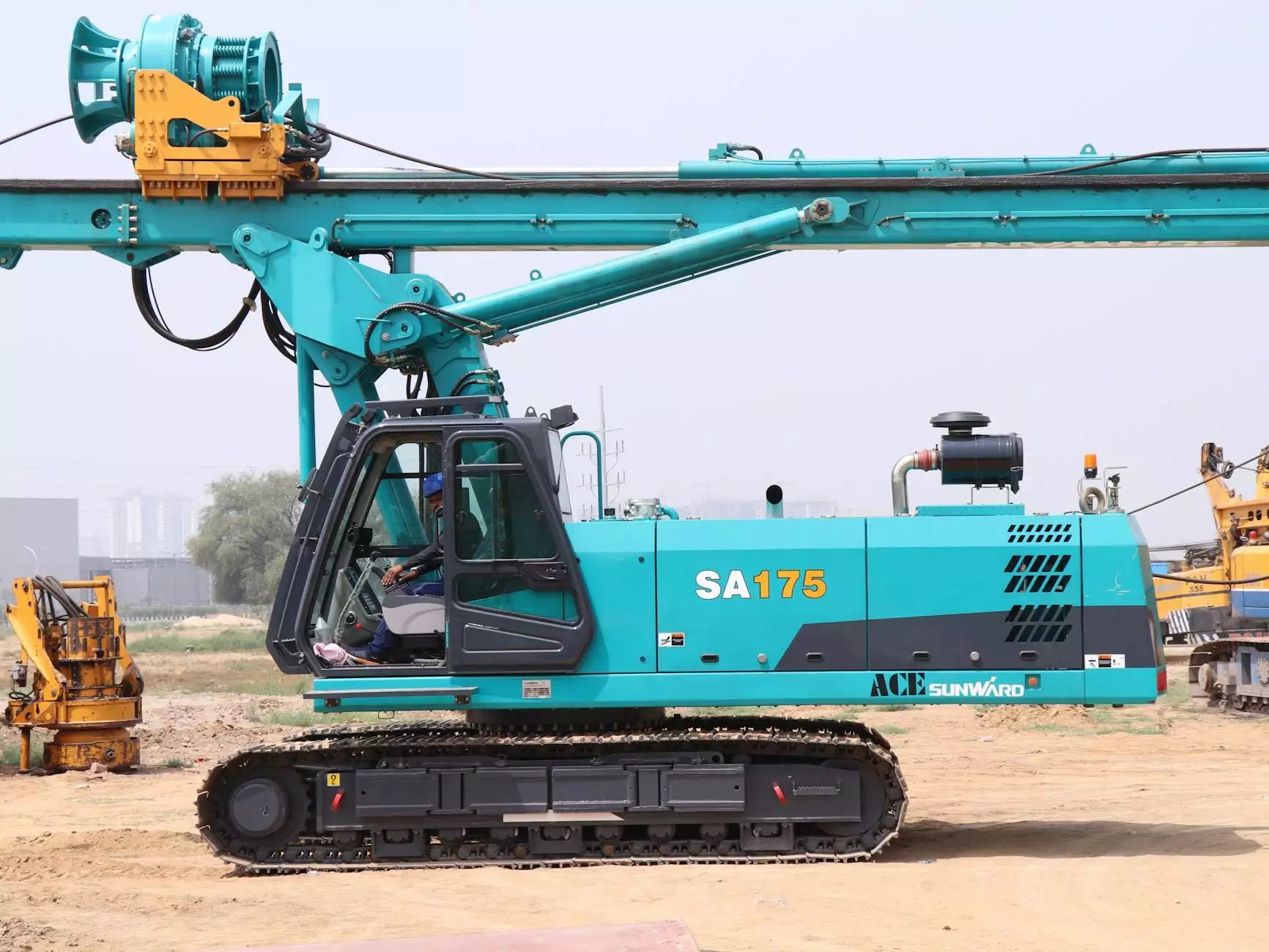
In today's fast-paced manufacturing world, the need for precision and efficiency is paramount. One of the key technologies that have revolutionized the manufacturing process is cnc machining. A cnc machining factory specializes in this technology, ensuring that products are manufactured with the highest standards of accuracy and repeatability.
What is CNC Machining?
CNC, which stands for Computer Numerical Control, refers to the use of computers to control machine tools. This includes everything from lathes to milling machines. By employing this technology, a cnc machining factory can produce complex parts with intricate designs that would be impossible or too costly to create using traditional machining methods.
Benefits of CNC Machining Factories
The advantages of utilizing a cnc machining factory are numerous and impactful to various industries.
1. Precision and Accuracy
- High Tolerance Levels: CNC machines can achieve tolerances of as low as ±0.001 inches, which is critical in industries like aviation and medical devices.
- Consistency: Once a design is programmed, every produced part will be virtually identical, eliminating human error.
2. Efficient Production
- Speed: CNC machines can operate continuously and can be programmed to work on multiple materials, significantly increasing production speed.
- Reduced Labor Costs: Automation decreases the need for manual labor, thus reducing overall costs.
3. Versatility
- Material Capability: A cnc machining factory can work with a variety of materials including metals, plastics, and composites.
- Design Flexibility: Designs can be easily modified with minimal downtime, making it perfect for prototyping and small-batch production runs.
The CNC Machining Process Explained
Understanding the CNC machining process is crucial for anyone considering utilizing a cnc machining factory. Here’s a step-by-step breakdown:
1. Design Creation
The process begins with creating a detailed CAD (Computer-Aided Design) model. This model serves as the blueprint for the parts to be produced.
2. Programming
The CAD model is then translated into a CAM (Computer-Aided Manufacturing) program. This involves assigning numerical values for machine movements and controls.
3. Machine Setup
Machinists prepare the CNC machine by installing the necessary tools and loading the raw materials needed for production.
4. Machining
Once the machine is set up, it begins the machining process, cutting the material into the desired shape based on the programmed instructions.
5. Quality Control
After machining, the parts undergo quality control inspection to ensure they meet the stringent requirements set by the client.
Industries Benefiting from CNC Machining Factories
The impact of cnc machining factories extends to multiple sectors, enhancing production efficiency and product quality.
Aerospace Industry
In the aerospace sector, precision is crucial. Parts like wing brackets and turbine components often rely on the high accuracy that CNC machining provides.
Automotive Industry
The automotive industry uses CNC machining for producing a variety of components such as transmission parts, engine blocks, and custom fittings, significantly speeding up the manufacturing process.
Medical Devices
From surgical instruments to prosthetics, the medical device industry demands precision and reliability, making CNC machining an invaluable resource.
Consumer Electronics
CNC machining is pivotal in the production of housings and internal components for devices like smartphones and laptops, where design and accuracy are key.
Future Trends in CNC Machining
As technology advances, cnc machining factories will continue to evolve. Here are some trends to watch:
1. Increased Automation
Integration with robotics and AI will further enhance efficiency in CNC machining, allowing factories to operate autonomously and reduce labor costs.
2. Advanced Materials
As new materials emerge, CNC machining will adapt, providing solutions for manufacturing with complex alloys and composites.
3. Eco-Friendly Practices
With growing concerns over environmental impacts, cnc machining factories are likely to adopt more sustainable practices, focusing on reducing waste and energy consumption.
The Importance of Choosing the Right CNC Machining Factory
When it comes to selecting a cnc machining factory, several factors should be considered. Quality, experience, and technological capabilities are paramount.
1. Quality Management Systems
Opt for factories that have established quality management systems (QMS) such as ISO 9001 certification, which ensures they adhere to high standards.
2. Experience and Specialization
Different factories may specialize in various sectors. Look for those with expertise aligned with your specific needs.
3. Technological Advancements
Select a factory that invests in the latest CNC technology. This not only enhances performance but also ensures the best outcomes for your projects.
Conclusion: The Strategic Advantage of CNC Machining Factories
In conclusion, cnc machining factories play a critical role in the modern industrial landscape. Their ability to produce high-quality, precise components quickly and cost-effectively provides businesses with a strategic advantage in competitive markets.
As we move into the future, embracing advancements in technology and sustainable practices will be essential for these factories to meet the evolving demands of industries worldwide. Whether you operate in aerospace, automotive, or medical sectors, leveraging the capabilities of a skilled CNC machining factory like DeepMould can position your business for success.